
ABURA O URU
to sell oil
In old Japan, there were roadside merchants who specialized in the selling of oil for cooking and other household purposes. Even then, cooking oil was a low-margin commodity. Therefore, this occupation did not provide a very high level of income.
There are no longer roadside oil merchants in Japan, but the phrase abura o uru has become a metaphor for any low-value-added activity. The expression usually refers to office workers who putter about doing meaningless tasks, or spend too much time at the coffee machine or in the smoking area.
"Selling Oil" and the Japanese Working Style
Early in my career as a corporate samurai, I took a job at the Chicago branch office of a division of Mitsubishi. It wasn’t long before I noticed something peculiar about the working style of my Japanese coworkers: They often mixed legitimate work activities with socializing, reading the paper, and other leisurely pursuits. I was especially puzzled by this behavior in light of the long hours which they spent on the job. As I was guiltily taking my leave at 5:15 p.m., my Japanese coworkers would still be at their desks. Some of them were busy tapping away at their keyboards or making deals over the phone with clients; but at least one or two would be unfolding a copy of the Daily Yomiuri (a Japanese newspaper) across his desk.
This made no sense to me at all: I preferred to work full bore while I was in the office, and then leave as soon as reasonably possible. I had no desire to linger at my desk and read the paper.
I asked one of my colleagues, Mr. Ohno, why the Japanese punctuated their workday with so many breaks, at the apparent cost of spending addition time in the office. According to Mr. Ohno, staying in the office for eleven to thirteen hours per day was simply part of the company’s culture. And while this much was expected, the company also understood that its employees weren’t machines. They needed a few minutes here and there to recharge their batteries. He also pointed out that for most Japanese, the workplace is like a second home. They enjoy spending time on the job with their colleagues, and therefore don’t watch the clock like so many American employees do.
Finally, since ours was an overseas branch office, some employees had to stay late to telephone the main office in Japan (though almost no one had to do this everyday.)
No Slack Time in the Factory
While office workers may occasionally engage in “oil selling,” the production workers in Japanese factories have no such luxury. The influence of unique manufacturing philosophies such as kaizen (カイゼン ) and the Toyota Production System (TPS) have made Japanese production workers ultra-efficient.
Japanese plant managers and efficiencies experts constantly examine processes to eliminate waste, or muda (無駄). Japan is the birthplace of so-called “lean production.” This means that every process cycle time must be shaved to its absolute minimum, and every machine, raw material input, and worker must be employed in the most efficient manner possible.
The constant enhancement of worker productivity is an important issue in Japan, for a number of reasons. Japanese industry has always had to do more with less—smaller factories, fewer natural resources, etc. In the next few years, Japanese companies will also face a demographic challenge: Declining birthrates have resulted fewer people are entering the workforce. Therefore, businesses will have to learn to be more productive with the workers that they have.
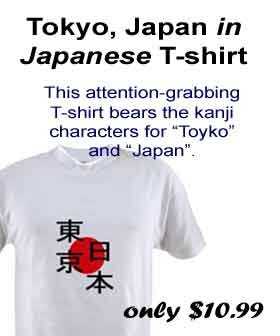